Abstract
Robotic Wire Arc Additive Manufacturing (WAAM) is a high-rate metal additive process suited for rapid prototyping and repair, but it often suffers from geometric inaccuracies—especially with high thermal conductivity materials like aluminum. This paper presents an in-situ, multi-robot, multi-sensor WAAM framework for real-time sensing and welding optimization. A co-located line scanner enables geometry sensing during deposition, while a secondary robot with a thermal camera provides temperature feedback. We propose a coordinated motion planning strategy and compare several welding models, including analytical, neural networks, and Gaussian processes. Experiments demonstrate that our in-situ system achieves comparable accuracy to turn-by-turn methods with greater efficiency, with neural networks offering the best trade-off between accuracy and scalability. Ongoing work focuses on incorporating additional sensing information to further enhance optimization and modeling.
Project Video
Results
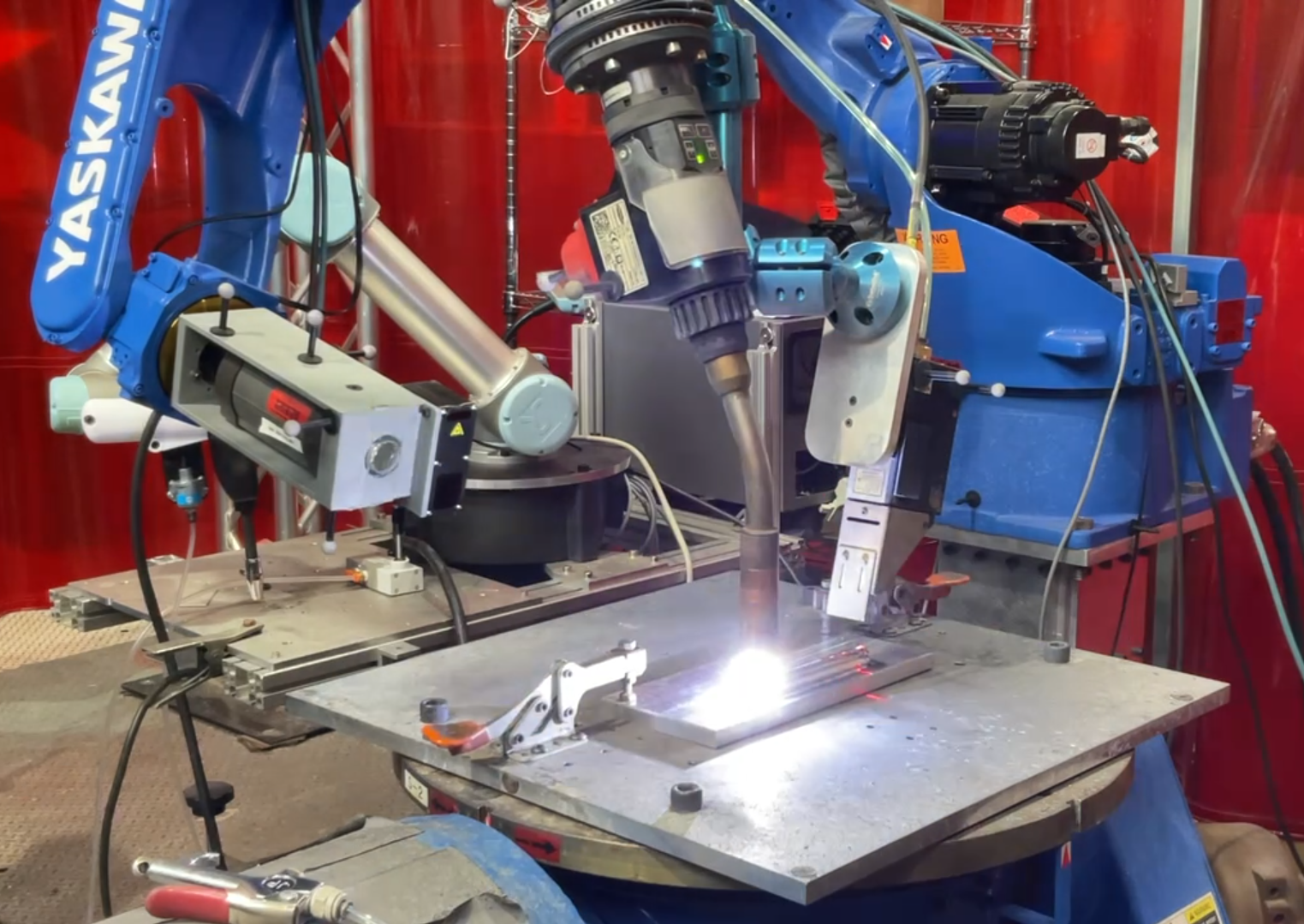
The multi-robot multi-sensor testbed. The welding robot is equipped with a co-located line scanner, FujiCam. The second robot is equipped with a thermal camera, FLIR.
Framework
During operation, the robots simultaneously perform welding and collect sensor data. Sensor outputs—such as thermal images and line scans—are pre-processed to extract relevant parameters, including weld pool temperature and weld bead geometry. Combined with the recorded welding parameters and robot motion data, this information is used to update a model that captures the implicit dynamics of the welding process.
WAAM Performance Evaluation
We compare the proposed in-situ sense-print system to a turn-by-turn scan-and-print method [3] and an open-loop baseline. The welding material used is ER4043, an aluminum alloy characterized by low melting point and high thermal conductivity, which makes it prone to defects and porosity. In-situ sense-print performs comparably to the turn-by-turn method and significantly outperforms the open-loop baseline.
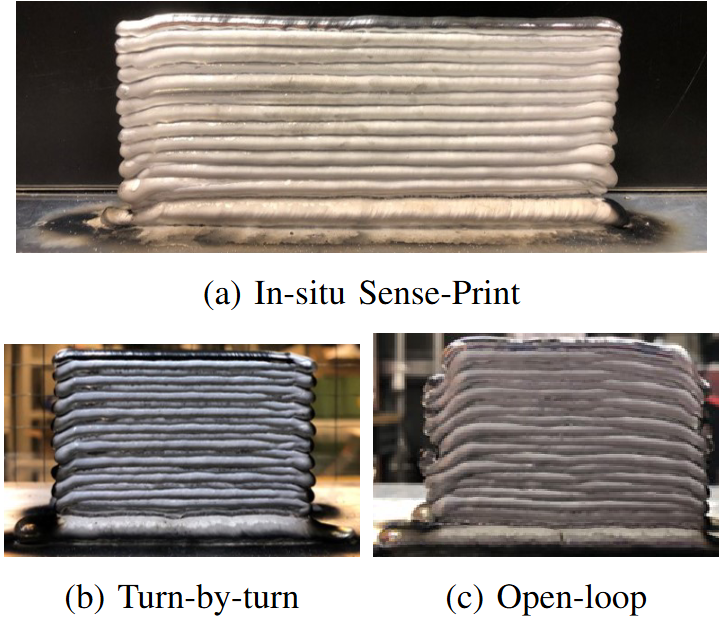
Welded wall comparison: in-situ vs. turn-by-turn vs. open-loop.
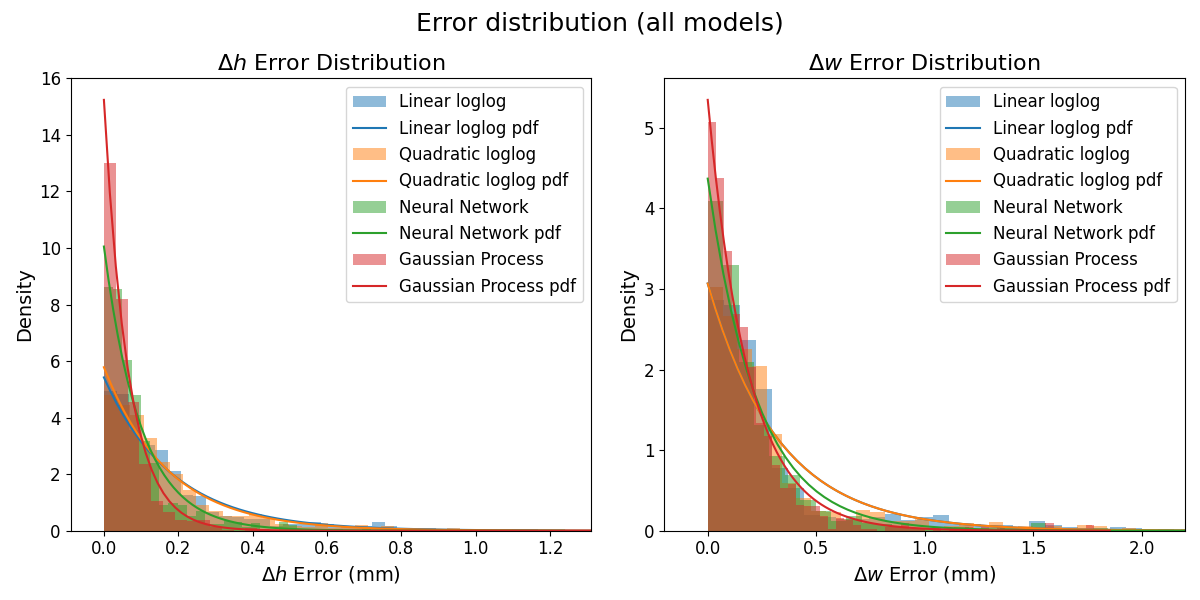
WAAM Model Accuracy
We evaluate prediction performance for NN, Gaussian Process and analytical models. Analytical models provide reasonable accuracy with minimal training cost, but both the NN and GP models offer significantly improved predictive performance. The GP model achieves the lowest training error, but tends to overfit and scales poorly. NN is the best trade-off between accuracy and scalability.